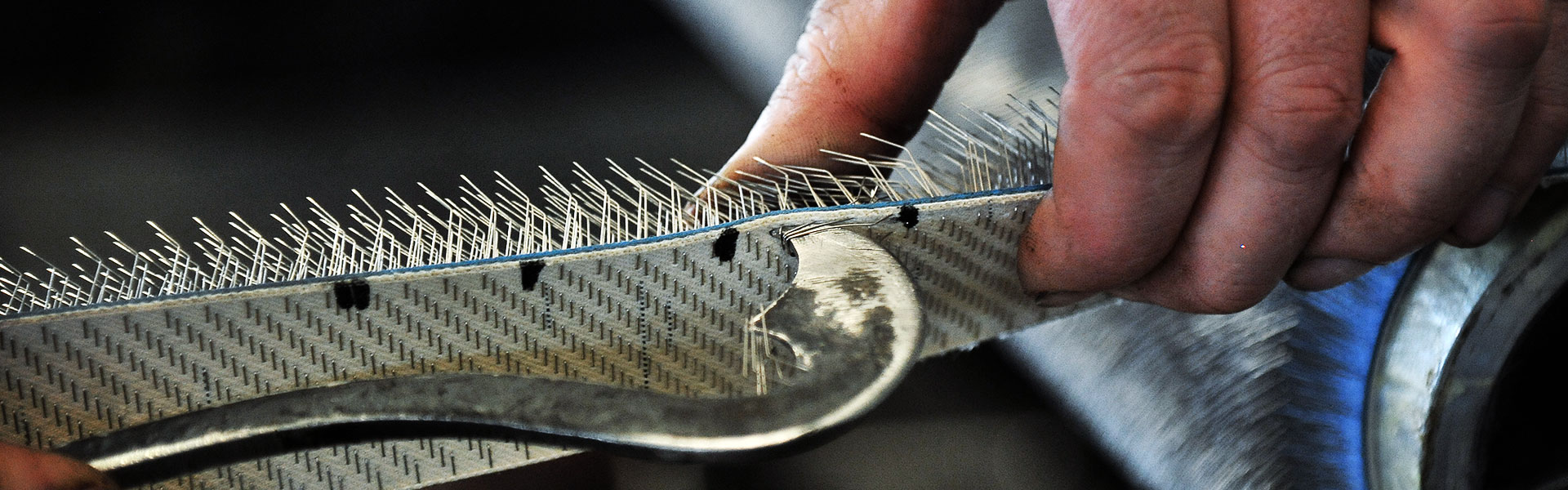
As every spinning technician well knows, the quality of a yarn produced by any type of carding set is deeply influenced by the condition of the fillet with which it is clothed. Proper maintenance of clothing allows steady efficiency and longer life with consequent savings when such important capital intense accessories are replaced. Clothing maintenance is carried out whenever it has to be cleaned and whenever it has to be ground.
As regards cleaning, we recommend only original products, such as our hand cleaning cards, which have specifications suitable to the clothing to be cleaned according to wire diameter, density and cleaning angle.
Accessories for maintenance
-
Setting gauges
-
Cleaning card
-
Cleaning card metallic holder
-
Manual grinding stone
-
Cleaning card wood holder
-
Cleaning card wood holder
As regards grinding, we strongly recommend that the intensive use of the long grinding roller or of any other device suitable only for plain grinding of clothing should be avoided. Because even though it achieves a perfectly smooth surface of the clothed roller, such an operation causes the teeth to lose the finishing with which they are delivered and this in turn can often cause problems of neps or of unsatisfactory carding, in particular with fine and very fine fibre processing.
Alternatively we do recommend the use of our two-motor grinding device, the first motor for the translation of the grinding head and the second for the rotation of the grinding wheels or of the discs installed on the grinding head. Such a characteristic allows more effective maintenance thanks to the high rotation speed of more than 3500 r.p.m.. Moreover, thanks to the special construction properties, with two high-resistance cylinders ground and with very low deflection, then undesired vibrations are avoided and it is possible to carry out side grinding and polishing operations which otherwise would not be possible with other types of equipment.
The following instructions are approximate as the mounting of flexible card clothing is greatly influenced by the experience of the technician in charge, by the type of mounting device, the environmental conditions and other factors. Below are some general recommendations on the fitting and mounting of flexible card clothing.
We would also like to remind all our customers that our company is available to give a mounting and flexible card clothing maintenance service (top and side grinding and brush polishing) with our specialized technicians with competitive conditions.
Generally speaking in order to erect new flexible card clothing the main operations are as follows:
- Remove the existing card clothing;
- Carefully clean the surface of the naked roller with some emery band paper, by turning it at normal speed;
- Check that all the mechanical parts, such as bearings, bushes, rings, etc. are in good working conditions;
- Fit the mounting device on the carding set or on the bench (the technician has to be sure that the equipment is in good mechanical working condition, that the mounting tension bar flexibility is acceptable, that the tension measuring device of the mounting tension bar gives correct information, and that the winch is correctly functioning);
- Carefully spread the surface of the cylinder with a very thin film of linseed oil. It is important that the oil amount is uniformly distributed on all the surface of the cylinder. In order to achieve this target every erector has his own system, we suggest to use a piece of nylon fabric ( e.g. about 1 meter wide and 2 meters long for swift and doffer) and cover partially the roller after dropping the oil on its surface. Then the roller should turn and the nylon will help to achieve uniform oil distribution. It is important to let the roller turn until the very beginning of the mounting operation, otherwise the oil will pour downwards and there will be parts with different oil thickness;
- Begin to mount the card clothing according to the technician's experience, we have reported at the end the list of our suggested erection tensions;
- In order to achieve a good result it is important not to stop the winding of the card clothing on the roller until completion, in order that it is as regular as possible.
- As soon as the fillet is fitted, clean it with a cleaning card (take special care during this operation if the fillet is on felt foundation);
- Make a grinding operation very softly by hand, with a hand grinding stone in order to equalize the various spirals of the fillet ;
- Clean one more time the fillet teeth with a vegetable brush.
- Foundation on 9 ply felt or rubber (swift of the 1st carding group): approx. 4/4.5 Kgs. per each mm. of fillet width. For example if the fillet is 60 mm. wide, the erection tension should be approx. 270 kgs.
- Foundation on 7 ply felt or rubber (if swift): approx. 3,5/3,8 Kgs. per each mm. of fillet width.
- Foundation on 7 ply felt or rubber (for all the other rollers, besides the swifts): approx. 3.2/3.5 Kgs. per each mm. of fillet width.
- Foundation on 5 ply rubber (for fancy rollers): approx. 2.5 Kgs. per each mm. of fillet width.
- card clothing mounting bar composed of a sliding structure in finned steel pipe and a distribution carriage for card clothing, equipped with a tested tension meter. The carriage can be moved manually or with a motor drive, due to its structure with 12 bearings it has a remarkable smooth sliding facility and perfect stability;
- winches with standard mandrels equipped with inverter controlled motors to fit different rollers, with variable speed for perfect matching of coils during assembly;
- mounting and grinding benches, with motor, and adjustable supports to suit different working widths and produced so as to assemble equipments easily and accurately.